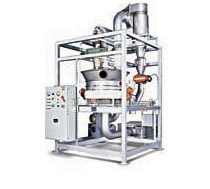
Kason self-contained system with circular fluid bed processor
Giá bán: Liên hệ
Hãng sản xuất: Tomoe Vietnam
Danh mục: Máy móc & Hệ thống
Nhà cung cấp: Anh Nghi Son
Xuất sứ:
Bảo hành: 12
Fluid Bed Dryers, Coolers, and Moisturizers
For bulk foods, pharmaceuticals, and chemicals.
Description
Because the circular fluid bed processor is also more compact, complete fluid bed systems can be pre-engineered and pre-configured on caster-mounted frames, ready for installation and start up.
Moreover, Kason circular fluid bed processors maintain an unprecedented level of operating efficiency across a wide range of model size ---from 18 to 84 inches (450 to 2125 mm) in diameter --- for laboratory and pilot plant testing as well as batch or high-volume in-line drying, cooling, or moisturizing of bulk foods, pharmaceuticals, and chemicals.
Features
- Inherently rigid, a Kason circular fluid bed processor does not require heavy steel sidewalls or cross braces to withstand extensive vibration.
- A Kason circular fluid bed processor uses a lighter gauge shell and components, with fewer weld seams, and requires only one air inlet and outlet resulting in lower material and labor costs.
- This self-contained fluid bed systems are lab tested using your material, engineered, and configured on a frame to ensure on-spec performance as delivered..
- Compact and lightweight, a complete Kason circular fluid bed system can be frame-mounted with casters for low cost shipping, easy installation, and in-plant mobility.
- With no internal cross members, fewer seams and corners, and a quick disconnect shell, a Kason circular fluid bed processor cut cleaning time dramatically.
Principle of peration
Continuous air flow and vibration separate and fluidize individual particles, maximizing the surface area of material and, accordingly, the rate at which drying, moisturizing, heating, or cooling can occur.
To prevent the uppermost layers of fluid bed particles from being pulled into the exhaust stream, the fluid bed exhaust plenum tapers outward to a longer diameter than that of the fluid bed screen surface, effectively reducing the air velocity by 50 percent.
The vibratory motion of the processor also serves to convey the material along a defined pathway for uniform processing on a "first in/first out" basis, and to evacuate the fluid bed at the end of each cycle.
To fit your material application and integrate with existing plant equipment, TOMOE offers a comprehensive range of equipment available as components, sub-systems, or complete systems as described below.