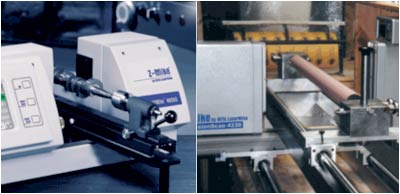
Z-Mike
Giá bán: Liên hệ
Hãng sản xuất: NDC Technologies
Danh mục: Thiết bị trong dây chuyền sản xuất
Nhà cung cấp: Anh Nghi Son
Xuất sứ:
Bảo hành: 0
Z-Mike
Precision Dimension Measurement Systems
Z-Mike bench-top dimensional measurement systems provide fast, accurate, and repeatable measurement of parts. This laser measurement device does not touch the product, thereby eliminating part distortion and operator influence which can affect measurements. The Z-Mike gauges can either be used in a Quality Control (QC) laboratory or on the plant floor to measure a range of part types and part dimensions. Dimension measurements include diameter, multiple ODs, TIR, taper, and part position. The Z-Mike gauges are available in four different models and provide a measurement range of 0.001 to 2.0 in. (0.0254 to 50 mm) with linearity as low as ±0.000020 in.
- The Z-Mike line also includes the PrecisionScan laser gauges for applications where a bench-top
solution is not required. - A variety of Modular Fixtures are available for any gauging need to properly hold workpieces.
Measure parts with the highest accuracy. (Click image to view)
Patented optical design and edge-sensing electronics provide high-precision measurements. Auto-compensation features maintain accuracy throughout the measurement range and adjust for thermal expansion outside laboratory environments.
Get reliable measurements from run to run.
Non-contact measurement technique provides the same level of accuracy, regardless of operator. Tolerance checking alerts operators of out-of-tolerance conditions. Mounting fixtures ensure the test piece is always properly presented to the gauge.
Easy-to-use features. (Click image to view)
Touch-screen design and color graphical display provides a simple, yet powerful user interface. Use the library list to store product recipes and quickly, easily access product types. Several I/O ports provide flexible integration with other devices.
The Z-Mike gauges are proven performers in a wide range of industries. These gauges are designed to provide accurate and repeatable measurements of parts. Industry applications include:
- Small Motor Crankshafts
- Camshaft Lobes
- Crankshaft Bearings
- Cutting Tools
- In-line Cordless Drill Shafts
- Center-less Grinding
- Bar Polishing
- Pin Gauges
- Catheters & Guide Wires
- Meat Casings
- Copier and Rubber Print Rollers
- Can Punches and Dies
- Battery Cans
- ID & OD of Steel Tubes Reducing Dies and Mandrels
- Cold Metal Tubes
- Hot Products
- And more...
Diameter Measurement
Outside Diameter of the lobe on a camshaft is determined by the shadow created when the shaft obscures the laser beam as it scans across the measurement area. The camshaft is mounted on a linear slide so that the outside diameters can be determined for each cam.
Ovality Measurement
A rubber print roller is manually rotated to measure the maximum and minimum diameter. Ovality is displayed as Max OD – Min OD.
Effective Cutting Diameter
The effective diameter of a part is determined by rotating it in a fixture with near-zero runout. The position of the part and its diameter are monitored simultaneously as the part rotates to determine the maximum circle inscribed by the part.
Taper Measurement
The taper angle of a crankshaft bearing is determined by traversing the part on a linear slide with an encoder. The OD is measured at two locations and taper is determined by calculating the change in diameter divided by the change in position of the slide.
TIR Measurement
A cutting-tool blank is rotated on a V-block while measuring the gap between the blank and a reference edge. TIR is measured as the total change in the size of the gap.
Inner Diameter Measurement
The inside diameter of a tube forming die is measured by traversing the die across the scanning field. As the die is traversed, the software looks for the “peak” or maximum size of the inner light segment. This system can measure dies from as small as 0.5” ID to 5.5” ID without any changes to the fixturing or configuration.
- The following technical information provides a range of performance data across all models.
For specific product details to meet your unique application needs, please refer to our data sheets. -
- Measurement Range: 0.0254 to 50 mm (0.001 to 2.0 in.)
- Repeatability: to ±0.13 μm (±0.000005 in.)
- Linearity: as low as ±0.5 μm (±0.000020 in.)